How to Strengthen Sheet Metal Parts
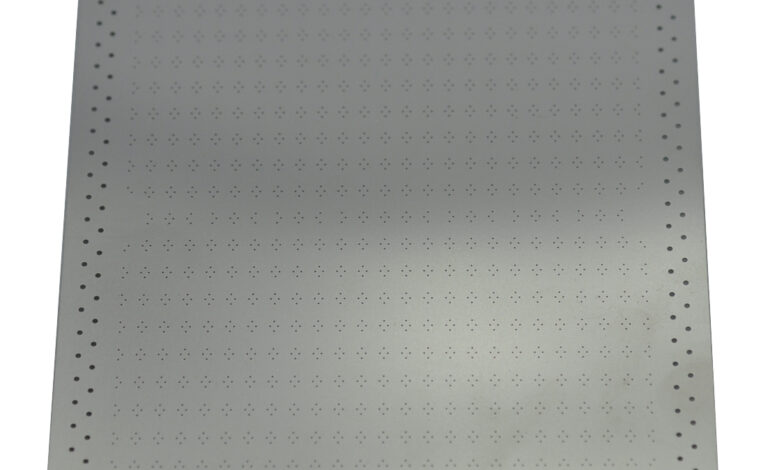
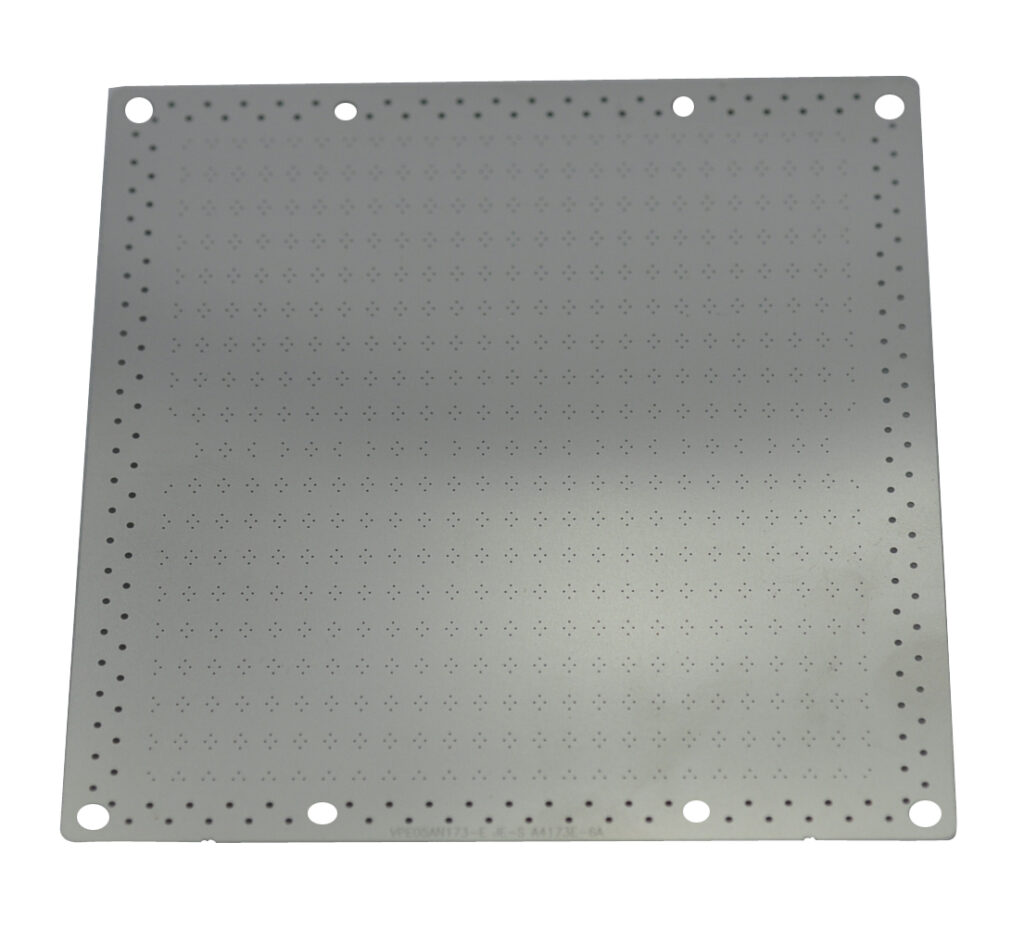
Among the many ways to reinforce sheet metal parts, bending can help them become stronger. You can bend the edges of thin strips of metal to change their shape, which will create a bulge in the panel. Depending on the size and shape of your panel, you can also use a hammer and a sandbag, or an English wheel to stretch the metal. The method you choose will determine how much work and time it will take.
Adding ribs and grooves to sheet metal parts can help them retain tension and add design to them. Ribs are most effective on copper and brass. While they add visual interest to the panel, they also strengthen the material. Using a hammer to punch holes can help, but a small draw-through punch-flare is easier to use and can be much more accurate. By combining these two techniques, you can easily strengthen sheet metal parts and create attractive designs.
Another way to reinforce sheet metal parts is by folding the edges. This will give them an instant structural integrity and minimize the likelihood of deformation. The amount of bend depends on the application and fitment of the part. This method increases the thickness of the base material and makes it more rigid. It also eliminates the possibility of deformation. However, it’s important to consider how much you need to strengthen sheet metal parts before making any final decisions.
For flat sheet metal, bending can strengthen it, but be sure to follow a certain bend radius, as excessive bending can cause cracks. To avoid cracks, determine the minimum radius that you can bend the sheet without cracking it. You can also reinforce sheet metal parts by punching holes or slots in them. This will give them an added layer of strength and help them withstand more abuse. But be sure to consult with a production engineer before attempting this method.
Another option to reinforce sheet metal parts is welding. Welding joins metal parts with each other to form a metallurgical bond. However, this option is only needed when the product contains several components. For many applications, you can take advantage of sheet metal fabrication services from a trusted source like RMT. They have extensive knowledge in different materials and offer a variety of customization and fabrication options. There are many other benefits of using sheet metal, but these are the most important considerations.
Another way to strengthen sheet metal is through the use of rivets. Riveting can also be replaced by brazing. A MAPP gas torch and brass brazing rods are used to heat the joint. The brass is drawn into the joint by capillary action. In addition, hemmed seams can be used to join two edges. Another option for connecting two edges is a grooved seam. This seam uses grooves on opposite sides of the sheet metal, and the two edges overlap.
The thickness of the wall on a sheet metal part is very important. The wall thickness must be consistent throughout. The thickness of the bottom edge may be thicker than the sides, and vice versa. Trying to make a part thicker by welding two pieces together will not help. This will only add to the thickness of the part, and the costs of the project. And, you’ll need to redesign the part.
Another way to reinforce sheet metal parts is by adding bend reliefs. These are raised areas added to the edges of bends to prevent them from tearing or bending easily. They also prevent the sheet metal from buckling, and control the amount of deformation. The flange width must be approximately four times the thickness of the sheet metal. Depending on the design, a rectangular or tear-shaped bend relief will do.
If spot welds are not an option for you, POP rivets are another alternative. POP rivets are more cost-effective and require no welding, and you can also dress them easily with a ball peen hammer. Just be sure to use a steady hand and a proper size hammer to stamp the rivets properly. Also, don’t forget to use rivet sets, which are a better choice than spot welds.