Precision Metal Parts for Aeronautics
Suitable manufacturing process
To save costs while ensuring quality, more and more aviation designers are turning to MIM technology. More than 49,000 aircraft are expected to be produced worldwide by 2026, and MIM can support the huge component demand.
Just as composite fibres have replaced aluminium in fuselage and wing structures, and ceramics have replaced key engine components, MIM is replacing smaller, conventional metal machined parts. MIM is a mesh molding process for the production of solid metal parts that combines the design freedom of plastic injection molding with the excellent material properties near the forged metal.
MIM mixes a metal powder with a thermoplastic adhesive and moulds it into a cavity. The molded parts are heat treated (sintered) to remove the adhesive and produce a network of high density components. Because it is a molding process, it can produce an almost infinite number of highly complex 3D geometric shapes in many different metal alloys.
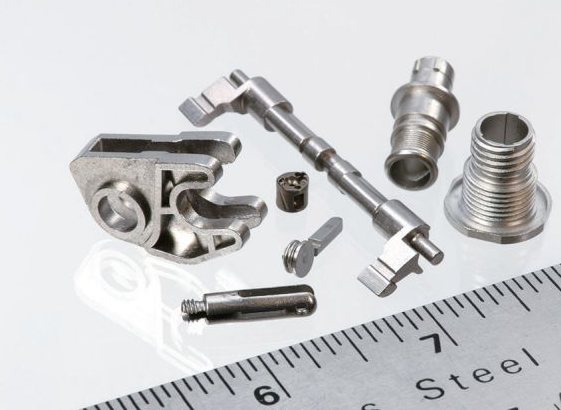
Manufacturing cycle
Metal Injection Molding (MIM) projects can take up to 16 weeks to complete, starting with mold design and construction. Once tools are set up, mass production of 2,500 or more can usually be completed in 4 weeks or less. Aircraft manufacturers need at least 10,000 starters per year. To ensure the number and timing of parts delivered each quarter, aircraft manufacturers should release no less than 2,500 to 3,000 units per quarter, three or four times per year. MIM is more consistent and reliable in terms of quality, price and on-time delivery than in-house or outsourced precision machining that requires parts.
The advantages of the MIM
Traditionally, aerospace manufacturers have used powder metallurgy (PM), injection molding, and precision machining to complete smaller part designs, but MIM offers several advantages.
MIM parts have greater metal density and three times the fatigue strength of PM parts. MIM parts also retain the tensile strength of the original material. In addition, PM parts are limited to 2D features, while MIM is able to meet complex aerospace geometry, including bottom cuts, holes perpendicular to the spindle, and 3D features.
Mims are typically lighter than precision-machined aerospace components. Often, excess material is left in parts to save processing time and reduce costs. The MIM digs out excess material, which saves part weight, manufacturing time, materials, and money in the final part cost.
At the same time, MIM parts also exhibit superior characteristics to injection molded parts in certain parts such as cockpit, seat assembly, and seat belts. Because MIM parts are conductive, magnetic, robust, rigid, chemical resistant, and maintain excellent performance at temperatures well above the melting temperatures of most polymers.
Application
MIM is an excellent choice when parts are sold in batches of more than 10,000 pieces, parts are 3 “or smaller, weigh no more than 25g but are of complex shape, and cost reduction is required. MIM is typically specified for use in a range of finish flexibility allowing for finishes and colors from matte stainless steel to highly polished finishes.
Lightweight is an aircraft design goal, and MIM technology is a powerful force to achieve this goal.